5 Important Factors to Consider When Selection of Spare Parts
Spare parts selection is a critical factor for the performance and continuity of your business. Choosing the right spare parts increases the efficiency of your operations while also reducing the risk of malfunction. Here are 5 important factors to consider when choosing spare parts:
1. Compatibility: It is important that replacement parts are fully compatible with your existing equipment. Compatibility in terms of measurements, connections and other technical specifications ensures trouble-free installation and functionality. Paying attention to manufacturer instructions and equipment specifications helps select the correct compatible replacement parts.
2. Quality and Reliability: The quality and reliability of spare parts affect the performance of your business. Choosing high-quality parts from a reliable manufacturer or supplier will ensure you get long-lasting and durable products. Reviewing evidence such as quality certificates and references is important for choosing the right spare parts.
3. Performance: The functionality and performance of spare parts have a huge impact on the efficiency of your operations. Choosing spare parts that suit your business needs increases process speed, safety levels and productivity. Examining performance data and references helps in choosing the right spare parts.
4. Cost-Effectiveness: Cost-effectiveness should be taken into consideration when choosing spare parts. It is important to choose not the cheapest option, but spare parts that provide an affordable balance of price and quality. Cheap or poor quality spare parts can lead to failure after a short time, increasing costs. Conducting long-term cost analyzes and evaluations helps you make the right cost-effective choices.
5. Supply Process: Providing spare parts on time is critical for business continuity. Working with a supplier that provides reliable and on-time delivery ensures that your business runs smoothly. Factors such as speed, flexibility and customer service of the procurement process should be taken into account. Evaluating the performance and communication during the supply process of spare parts helps you choose the right supplier.
Spare parts selection is critical to the success of your business. Choosing the right spare parts, taking into account factors such as compatibility, quality and reliability, performance, cost-effectiveness and procurement process, reduces the risk of failure while increasing the efficiency of your operations. To select spare parts that suit your business needs, it is important to seek expert advice, follow manufacturer instructions and review quality control processes. The right selection of spare parts allows you to secure your business and ensures a trouble-free operating process.
1. Compatibility: It is important that replacement parts are fully compatible with your existing equipment. Compatibility in terms of measurements, connections and other technical specifications ensures trouble-free installation and functionality. Paying attention to manufacturer instructions and equipment specifications helps select the correct compatible replacement parts.
2. Quality and Reliability: The quality and reliability of spare parts affect the performance of your business. Choosing high-quality parts from a reliable manufacturer or supplier will ensure you get long-lasting and durable products. Reviewing evidence such as quality certificates and references is important for choosing the right spare parts.
3. Performance: The functionality and performance of spare parts have a huge impact on the efficiency of your operations. Choosing spare parts that suit your business needs increases process speed, safety levels and productivity. Examining performance data and references helps in choosing the right spare parts.
4. Cost-Effectiveness: Cost-effectiveness should be taken into consideration when choosing spare parts. It is important to choose not the cheapest option, but spare parts that provide an affordable balance of price and quality. Cheap or poor quality spare parts can lead to failure after a short time, increasing costs. Conducting long-term cost analyzes and evaluations helps you make the right cost-effective choices.
5. Supply Process: Providing spare parts on time is critical for business continuity. Working with a supplier that provides reliable and on-time delivery ensures that your business runs smoothly. Factors such as speed, flexibility and customer service of the procurement process should be taken into account. Evaluating the performance and communication during the supply process of spare parts helps you choose the right supplier.
Spare parts selection is critical to the success of your business. Choosing the right spare parts, taking into account factors such as compatibility, quality and reliability, performance, cost-effectiveness and procurement process, reduces the risk of failure while increasing the efficiency of your operations. To select spare parts that suit your business needs, it is important to seek expert advice, follow manufacturer instructions and review quality control processes. The right selection of spare parts allows you to secure your business and ensures a trouble-free operating process.
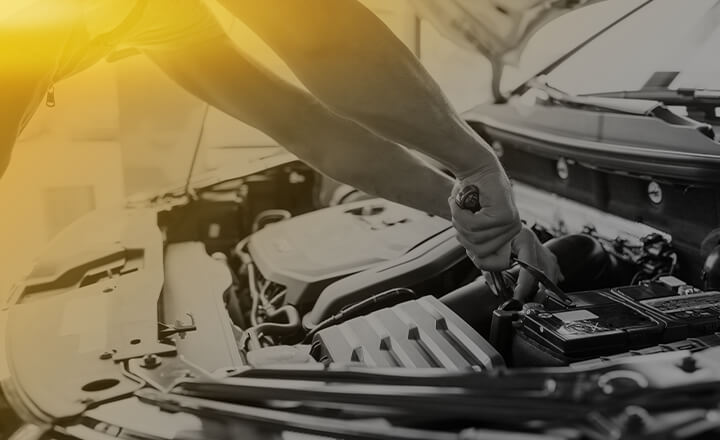